What is calibration of instrument? This is a question that many beginners in the field of instrumentation and measurement often ask. Calibration is a crucial process that ensures the accuracy and reliability of measurement instruments. In temperature calibration egypt this beginner's guide, we will explore the concept of calibration, its importance, and how it is carried out. Whether you are a student, technician, or someone with a general interest in the topic, this guide will provide you with a solid understanding of what calibration of instrument entails. So, let's dive in and demystify the world of instrument calibration.
Calibration of an instrument involves adjusting the readings of the instrument to calibration services ensure accuracy and precision. It is a process of comparing the measurements of an instrument to a known standard to detect and correct any deviations. Calibration is essential to maintain the quality and reliability of the instrument's measurements over time. It is commonly performed on various instruments such as thermometers, pressure gauges, and weighing scales to ensure they provide accurate and consistent results. Calibration of instruments is typically carried out by trained technicians using specialized equipment and techniques to ensure the instruments are functioning within specified tolerances.
Understanding the Basics of Instrument Calibration
calibration scale services
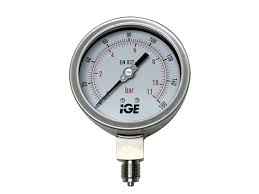
Instrument calibration is the process of checking and adjusting an instrument to ensure its accuracy and reliability. This is crucial in various industries such as manufacturing, pharmaceuticals, and healthcare, where precise measurements are essential for quality control and compliance with regulations. The calibration process involves comparing the readings of the instrument to known standards and making necessary adjustments to bring them into alignment. This may involve adjusting settings, replacing parts, or performing other maintenance tasks. Calibration is typically performed by trained technicians using specialized equipment and procedures. It is important to follow proper calibration protocols to ensure that the instrument meets the required accuracy and precision standards. Regular calibration is necessary to maintain the integrity of measurements and prevent costly errors or compliance issues. Companies often have established schedules for calibrating their instruments, and may also need to calibrate them after servicing or if they suspect a deviation in performance. Understanding the basics of instrument calibration is essential for anyone involved in using or maintaining instruments that require accurate measurements. This includes understanding the importance of calibration, the techniques and standards involved, best calibration laboratory and the potential consequences of inadequate calibration. By ensuring that instruments are properly calibrated, businesses can have confidence in the accuracy of their measurements and the quality of their products.
The Importance of Instrument Calibration in Daily Life
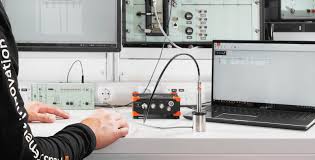
Instrument calibration is crucial in daily life for several reasons. First and foremost, calibration ensures the accuracy and reliability of the measurements taken by instruments. This is crucial in various fields such as healthcare, engineering, manufacturing, and scientific research. In healthcare, for example, calibrated medical instruments help in accurate diagnosis and treatment of patients. In manufacturing, calibrated instruments ensure the quality and consistency of products. Furthermore, instrument calibration is essential for compliance with industry standards and regulations. Inaccurate measurements can lead to costly errors and safety hazards, making instrument calibration an indispensable practice in daily life.
Calibration: Ensuring Accuracy and Precision in Instrumentation
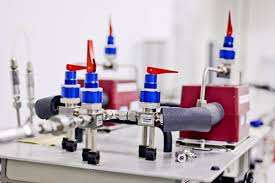
Calibration is the process of comparing the reading of an instrument with a known standard to ensure its accuracy and precision. This is done to make sure that the instrument is providing reliable and consistent measurements. Calibration is important in various industries, including manufacturing, healthcare, and environmental monitoring. It helps to maintain the quality of products, ensure the safety of processes, and comply with regulatory standards. Instruments that are regularly calibrated are more trustworthy and can help prevent costly errors or accidents. Calibration may be performed internally by trained personnel or by external calibration services that specialize in maintaining and certifying the accuracy of instruments.
Exploring the Science Behind Instrument Calibration
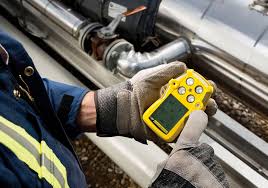
Exploring the science behind instrument calibration involves understanding the principles and methods used to ensure that instruments are accurately measuring and recording data. This includes understanding the concept of traceability, which ensures that measurements can be linked back to established standards. Additionally, understanding factors such as environmental conditions, human error, and technological limitations is essential in the calibration process. Calibration procedures typically involve comparing the readings of an instrument to known standards and making adjustments to ensure accuracy. This process is crucial in various industries, such as manufacturing, healthcare, and research, where precise measurements are essential for quality assurance and compliance. Understanding the science behind instrument calibration is important for maintaining the reliability and accuracy of measurement instruments.
The Step-by-Step Process of Instrument Calibration
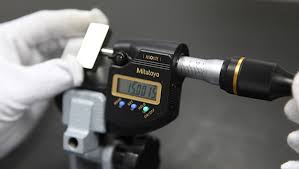
Instrument calibration is a step-by-step process that involves a series of measures to ensure the accuracy and precision of an instrument's readings. The process typically includes the following steps: 1. Establishing a Calibration Standard: This involves selecting a known and reliable reference standard that can be used to compare the instrument's readings. 2. Adjusting the Instrument: The instrument is adjusted to match the readings of the calibration standard. This may involve mechanical or electronic adjustments to bring the instrument into alignment with the standard. 3. Recording Calibration Data: The instrument's readings are compared to the calibration standard, and the results are recorded for future reference. 4. Performing Calibration Checks: Regular calibration checks are conducted to ensure that the instrument remains accurate and reliable over time. This may involve periodic recalibration or adjustments as needed. 5. Documenting Calibration Procedures: All calibration procedures, including the instrument's specifications, calibration standard used, and calibration dates, are documented to maintain a record of the instrument's calibration history. 6. Following Regulatory Requirements: If the instrument is used in a regulated industry, such as healthcare or manufacturing, it must adhere to specific regulatory requirements for calibration and documentation. Overall, the step-by-step process of instrument calibration is essential for ensuring the accuracy and reliability of measurements taken by the instrument. Calibration helps to maintain the quality of data obtained from the instrument and ensure it meets industry standards and requirements.
Common Instruments That Require Regular Calibration
Some common instruments that require regular calibration include: 1. Scales and balances used for weighing purposes 2. Thermometers used for monitoring temperature 3. Pressure gauges used for measuring pressure in various systems 4. Flow meters used for monitoring the flow rate of liquids or gases 5. pH meters used for measuring the acidity or alkalinity of a solution 6. Conductivity meters used for measuring the ability of a solution to conduct electricity 7. Gas detectors used for monitoring the presence of specific gases in the environment 8. Torque wrenches used for applying a specific amount of torque to fasteners 9. Force gauges used for measuring the force applied to an object 10. Particle counters used for measuring the concentration of particles in a fluid or gas.
The Role of Calibration in Maintaining Measurement Integrity
Calibration is essential in maintaining measurement integrity as it ensures that the measurements taken by a device or instrument are accurate and reliable. Calibration involves comparing the measurements of a device to known standards to identify and correct any inaccuracies. This process helps to maintain the accuracy and reliability of measurements over time. By regularly calibrating instruments and devices used for measurement, organizations can ensure that the results they obtain are trustworthy and consistent. This is particularly important in industries where precise measurements are critical, such as healthcare, engineering, and manufacturing. Calibration also plays a crucial role in quality control, as it helps to identify and rectify any deviations in measurement accuracy before they can impact the quality of products or services. Additionally, calibration records provide documentation of the reliability of measurements, which is often required for compliance with industry standards and regulations. In summary, the role of calibration in maintaining measurement integrity is paramount for ensuring accurate and reliable measurements and upholding quality standards in various industries. Regular calibration helps to identify and correct any deviations in measurement accuracy, thereby maintaining the integrity of measurements and instilling confidence in the results obtained.
Calibration Standards: What You Need to Know
Calibration standards are essential tools used to ensure the accuracy and reliability of measurement instruments and systems. They serve as reference points for calibrating devices such as thermometers, pressure gauges, and scales. When using calibration standards, it's important to choose the right standard for the specific parameter being measured. This may include factors such as temperature, pressure, volume, or electrical signals. Standards are typically traceable to national or international measurement standards to guarantee their accuracy. Regular calibration of measurement devices using standards is crucial for maintaining precision and consistency in data collection and analysis. It helps to minimize errors and ensure that results are reliable and reproducible. Many industries, including manufacturing, healthcare, and environmental monitoring, rely on calibration standards to meet regulatory requirements and quality standards. Overall, understanding the importance of calibration standards and knowing how to use them effectively is crucial for anyone working with measurement instruments and systems.
The Impact of Calibration on Industrial and Scientific Applications
Calibration is critical in industrial and scientific applications as it ensures the accuracy and reliability of measurement instruments and equipment. In industrial settings, proper calibration of tools and equipment like pressure gauges, thermometers, and flow meters is essential for maintaining consistent product quality and meeting regulatory requirements. In scientific research, calibration is crucial for obtaining precise and valid data in experiments and measurements. Failing to calibrate instruments accurately can lead to costly errors, faulty products, and compromised research results. Therefore, regular calibration of equipment is essential for ensuring the integrity and success of industrial and scientific applications.
The Future of Instrument Calibration: Trends and Technologies
The future of instrument calibration is heavily focused on advancing technologies and automation. This includes the use of mobile and cloud-based solutions for managing calibration processes, as well as the integration of Internet of Things (IoT) devices for real-time monitoring and adjustments. Additionally, the industry is seeing a trend towards the development of more accurate and reliable calibration standards, as well as the use of artificial intelligence and machine learning algorithms for predictive maintenance and calibration optimization. Overall, the future of instrument calibration is moving towards a more streamlined, efficient, and data-driven approach.